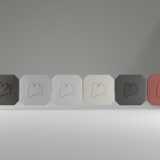
Challenge #5 – Leapfrog from 100% recyclable to 100% recycled
How to contribute to a more circular economy where everything is reused or recycled
Ready, steady… structure.
Recyclable and recycled sound similar, but there’s a big difference. A recyclable product has the technical characteristics to be reintroduced into the production cycles after processing. However, this doesn’t guarantee it will actually be recycled. And for the moment, a lot of products and packaging aren’t (yet) making a very circular journey. We could – and need to – do a lot more.
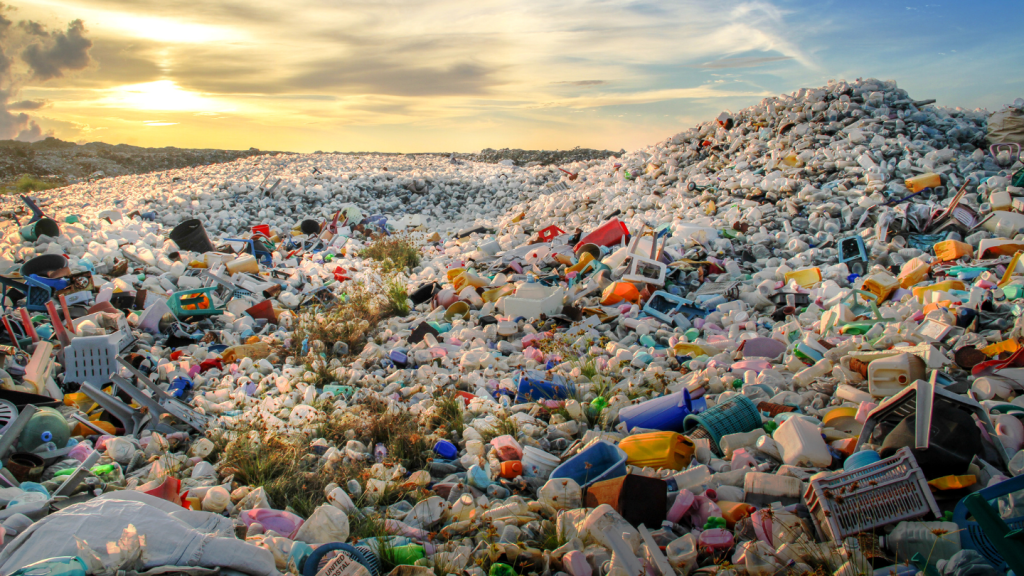
Turbocharging recycling rates and transitioning towards a circular economy requires big structural changes. It means shifting from a produce-consume-dispose model to a circular one where resources are reused and recycled whenever possible. And overhauling production, consumption and waste management processes – pretty much everything.
01. What’s at stake?
Saying goodbye to fossil fuels.
With fossil fuel resources dwindling and our planet heating up, now is the time to kick our dependence on oil. Promoting circularity – reuse, repair and recycling – limits the resources we need and our impact on the environment. But this shift is only possible with an integrated approach applied at every link in the value chain, from product design to end of life.
Product design
ensure products are easy to recycle or reuse at the end of their life cycle.
Recycling infrastructure
invest in technologies and facilities to efficiently process end-of-life materials.
Industry excellence & awareness
develop recycled materials to high performance standards – and get companies to use them.
02. Where we’re at?
Solutions & efforts by MATERI’ACT so far.
We’re already well and truly convinced that recycling is the key to a more circular approach – including low (or even zero) CO2 emissions. Our teams are on the case and working hard to develop materials that are recyclable and recycled – with a lot of help and inspiration from other innovators.
Recycled content.
All our products are recyclable. Many of our compounds and surface materials also contain recycled plastic (as well as biomass). Like NAFILean-R with a mix of hemp fibres and 100% recycled polypropene. We’re constantly looking for ways to add more recycled content to more products, while retaining the super properties that make the materials so useful. What’s more, we’ve chosen to focus on one type of plastic, polypropene, that is widely used (think shampoo and milk bottles) and recycled to make it easier to source and recycle at end of life.
The bigger product picture.
We could just look at the environmental impact of our products from sourcing to manufacture. We definitely do this. But we’re also interested in what happens when our compounds and surface materials are made into dashboard parts or leatherlike bags. That’s why we prioritize a monomaterial approach in our products, ensuring that end-of-life recycling is as straightforward as possible. We also work with partners and customers to recommend ways to make the final product easier to recycle. For example, when we teamed up with FORVIA to build the instrument panel of the Renault 5 e-Tech, we ensured the parts could be recycled, not just our NAFILean-R compound.
End of life – a new beginning.
As well as working with customers, we’ve teamed up with trusted recycling partners to secure a reliable supply of post-consumer plastic – as well as contributing to conversations and initiatives to improve recycling rates and facilities. We work hand in hand with Veolia in France and we’ve set up a joint venture with PCR Recycling in the United States (MATERI’ACT Dallas). Together (and only together), we can start to make circularity a reality on the ground.
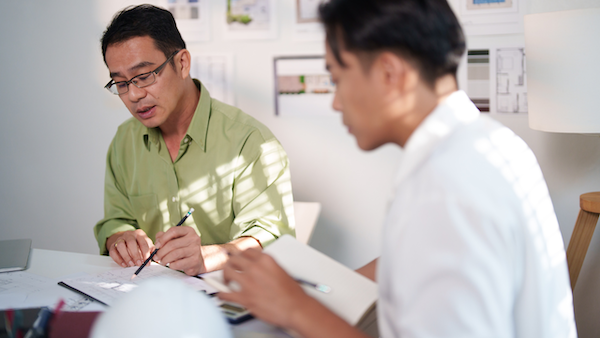
In focus : closing the mobility loop
Renault’s circular economy factory dedicated to mobility “Refactory” is home to GAIA. This subsidiary of The Future is Neutral pioneers automotive circularity by repairing electric vehicle batteries, reusing used car parts and… recycling materials for reuse in manufacturing.
GAIA organises the recycling of 3 materials including polypropene (that’s the plastic we use). So automotive equipment manufacturers can source 100% recycled technical polypropylene that meets automotive specifications, while incorporating plastic waste from end-of-life vehicles.
We’re delighted to contribute to this initiative and help close the loop with the automotive industry.
03. What’s next?
It takes a village to close the loop
To keep moving forward, we need change from the top down – and bottom up! Public authorities have a responsibility to implement policies that promote the circular economy. Like tax incentives for companies that use recycled materials and strict standards for products recyclability. At the other end of the spectrum, consumers need to know more about the circular economy and how each of their actions can contribute to more sustainable behaviours.
And in the middle, of course, we need efficient recycling technologies and facilities.
At MATERI’ACT, we’ll continue working closely with customers and recycling partners to make materials (and finished products) that are easier to recycle – and ensure they make it back into manufacturing processes. It goes without saying that we’re constantly looking for ways to integrate more recycled content and biomass to our materials too.
Keen to join us on this zero-carbon journey?
We’re always looking for new partners and customers to help us create fossil-fuel alternatives to high performance standards, which can be (and are) recycled
A few challenges on the way.
The road to net-zero and zero new plastic is going to get bumpy at times. But that’s the only road we care to take.
Wanna join us?
Pick a challenge you’d like to tackle with us.