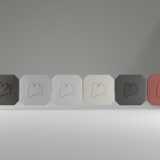
Challenge #4 – Get the environment into specs
How to shake up manufacturing to place environmental concerns at the heart of product design
Making room for net zero.
Industries, especially automotive, have strict standards relating to a multitude of requirements from performance to durability and safety – not to mention cost considerations to factor in. Adding additional criteria like carbon footprint, water use and recyclability into already densely packed specifications is no easy feat.
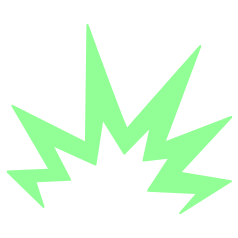
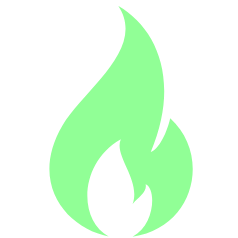
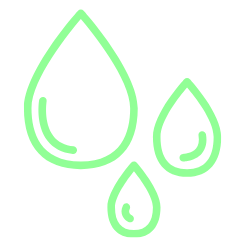
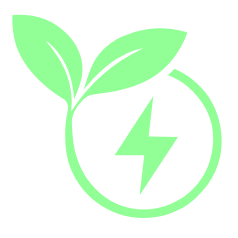
But necessary as design has such a massive impact on a product’s environmental footprint, from its weight to the choice of materials and manufacturing processes required – the list goes on. Taking these factors into account from day 1 is no longer optional if we want to reach net zero and develop a circular economy.
01. What’s at stake?
Let’s rewrite the rule book.
Many industry specifications have existed for decades. They have shaped manufacturing processes and have influenced sourcing choices. Each step in the value chain has been optimised to meet these requirements. Rewriting them takes time, investment and huge momentum. The good news? This momentum is slowly building as regulatory pressure grows and consumer expectations change.
Regulations, like the EU’s REACH (Registration, Evaluation, Authorisation and Restriction of Chemicals), impose tighter restrictions on certain substances – prompting manufacturers and designers to rethink the materials they use. At the same time, consumers are increasingly looking for “greener” alternatives, and manufacturers are keen to show they’re doing their bit too.
Attitudes are shifting, but there’s still a long way to go to drive concrete transformation.
source : PwC
source : OECD
Making environmental performance an asset – not an obstacle
To make this transition a reality in product design, there’s a long list of prerequisites. We need to make it easier for manufacturers make “eco-friendlier” choices. For example, easier to integrate more bio-based and recycled materials by boosting recycling rates and efficiency, as well as scaling recycled and bio-based feedstock. We need to convince manufacturers that environmental criteria aren’t an obstacle or hinderance. For example, by developing materials that combine high technical performance and competitivity with a lower ecological footprint.
The 3 Cs: clarity, coherence and coordination
But this isn’t enough. For impactful long-term change across industries, it is essential to clearly defining what we mean by “sustainable”, “eco-designed” or “low carbon”. Rolling out cross-industry definitions, certifications and regulations ensures everyone is on the same page and promises are backed up by figures and concrete impact.
Progress has been made. A number of sustainability certifications and labels already exist, like certified B-Corporation and Standard 100 by OEKO-TEX. Organisations like SGS and Bureau Veritas provide third-party carbon verification audits. The EU has created the Digital Product Passport. But it’s still a patchwork and lacks the international coordination and application to really shake up specifications on a massive scale.
02. Where we’re at?
Solutions & efforts by MATERI’ACT so far.
It goes without saying that we’ve prioritised the environmental impact of our products from the outset – that’s our raison d’être after all. But getting environmental criteria in industry specifications requires more, it means working with partners and customers to collectively change our ways of working and making sure we have the tools to define, trace and certify environmental performance.
A virtuous cycle – that doesn’t stop at delivery.
By integrating Life Cycle Analysis (LCA) into our processes, we explore the impact of our materials from sourcing to manufacture. We initially focused on CO2 emissions, but we also take in account other factors like water use. This means optimising our own processes and choosing our partners carefully (ideally local and like-minded).
But it doesn’t stop there. We also want to know what happens to our compounds and surface materials once they’re made into a product and when they are disposed of – making sure our materials are both recyclable and recycled. To do this, we work with customers to find ways to reduce the environmental impact of the final product and make recycling easier. For example, when working with FORVIA to create structural parts from NAFILean for instrument panel of the Renault 5 e-Tech. We also collaborate with recyclers to close the loop and source recycled feedstock; including end-of-life vehicles.
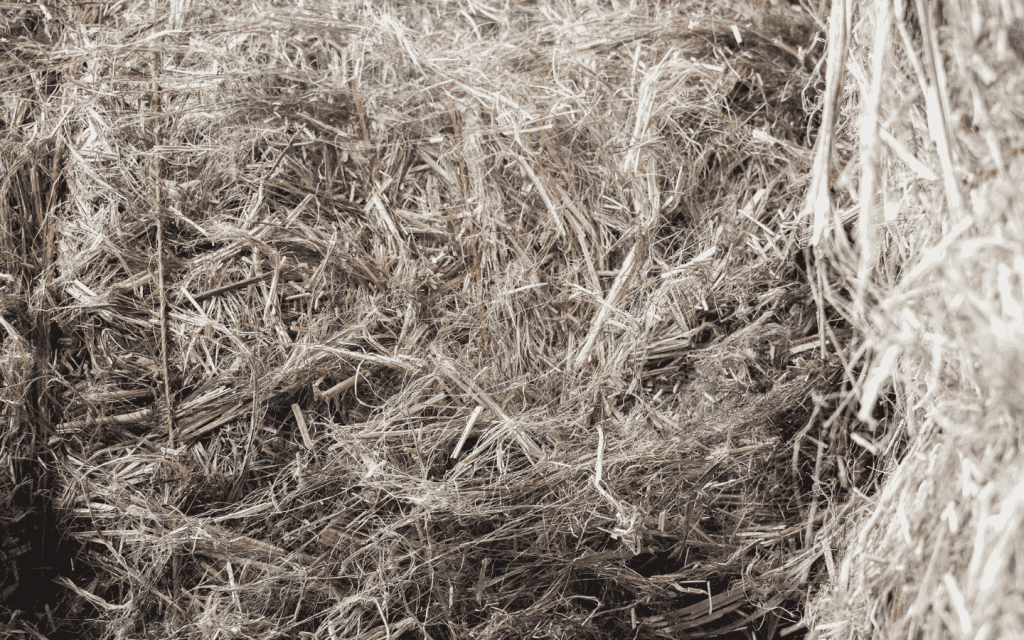
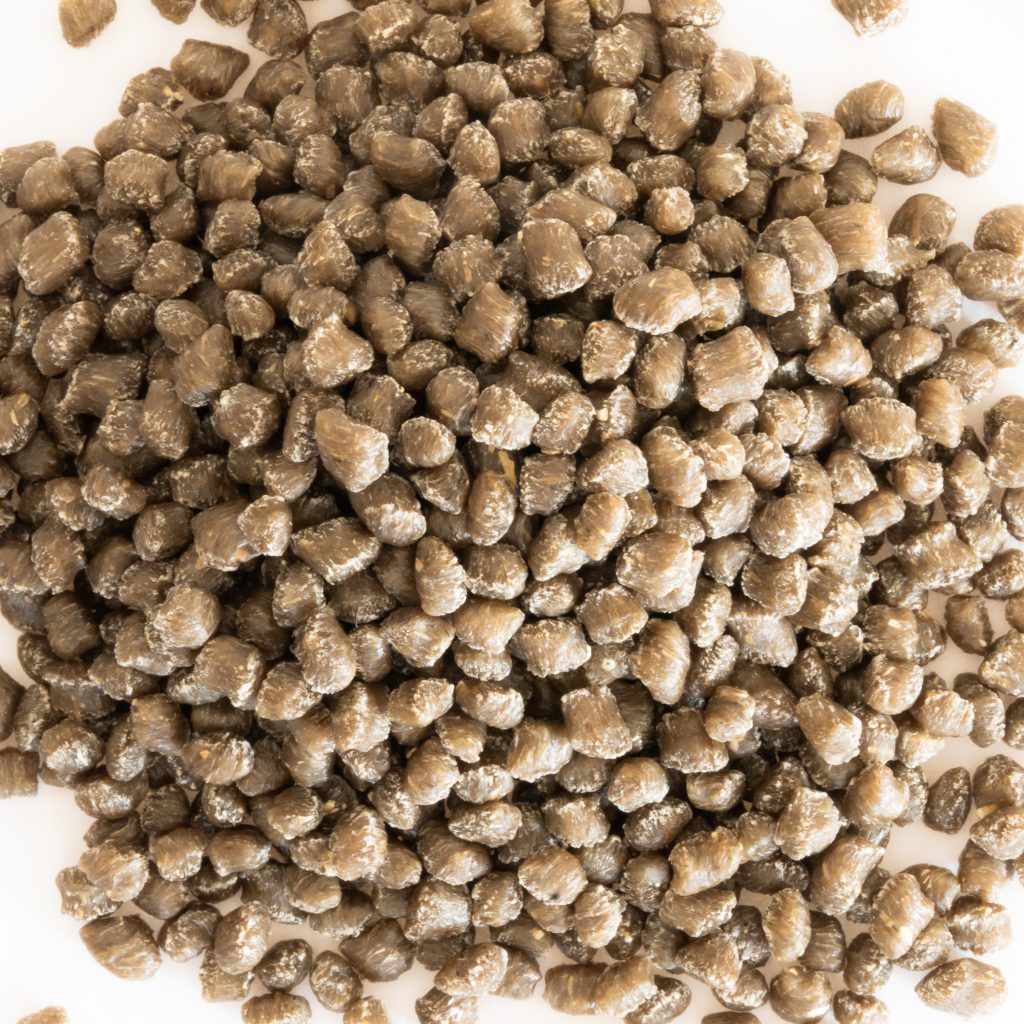
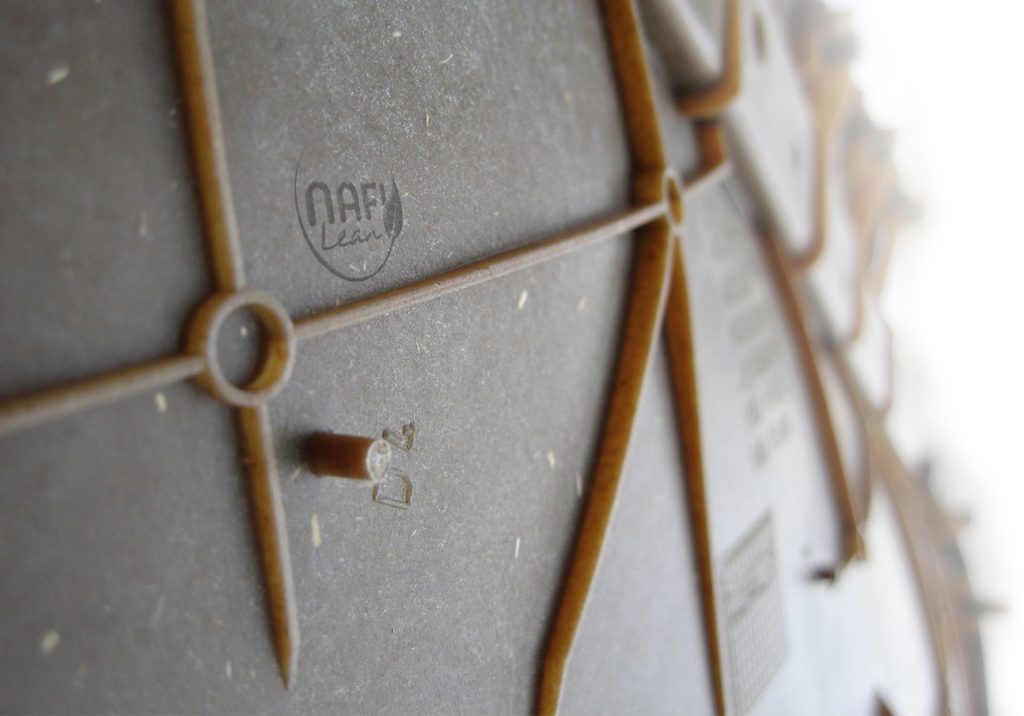
Providing proof
However, we can’t just say that our products are environmentally friendly. Customers and consumers increasingly expect detailed (credible) information to back up any claims. That’s why certifications are so important. We started by getting the Partial Environmental Footprint of 3 grades of NAFILean certified by SGS. We’ve also created Digital Product Passports for our plastic compounds to share essential information in an easy-to-access format. This is a starting point, but we’ve got lots more work to do!
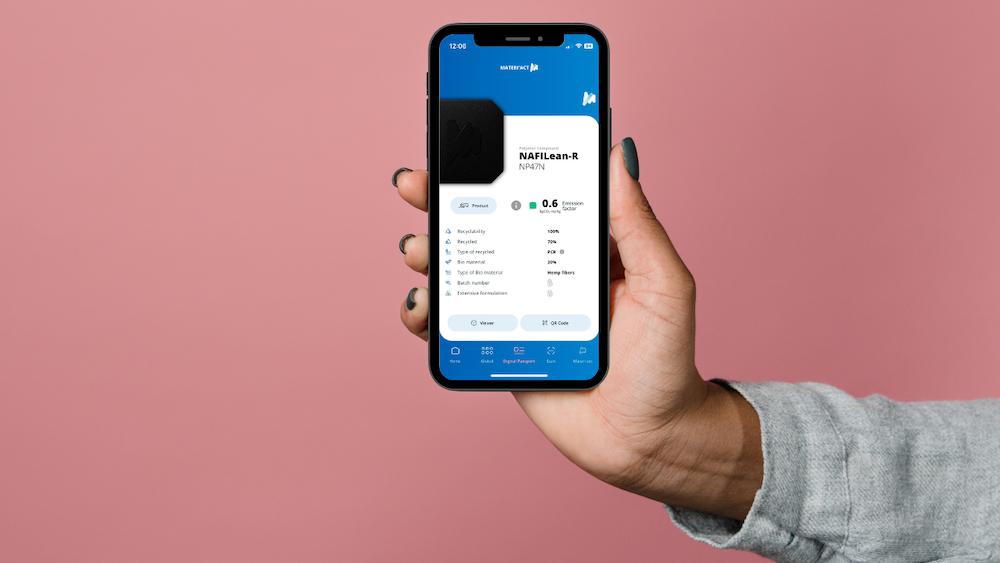
In focus : Digital Product Passport
The EU’s Digital Product Passport gives a detailed record of the product’s lifecycle to enhance transparency and ensure regulatory compliance. We’ve created DPP for all our plastic compounds.
- Easy QR-code access to data on all our plastic compounds
- Product Carbon Footprint for each material including recycled content
- Extensive Life Cycle Assessment with sustainability data & certificates
We’re now busy focusing on DDP for our other ranges too. Watch this space.
It doesn’t stop there.
We know it can’t go it alone. By establishing ongoing dialogue with manufacturers and customers, we want to contribute to conversations about (and concrete change to) the specifications that shape our ways of working. That’s also why we take part in industry-wide initiatives to support high standards for sustainable materials, like this collective call to uphold and reinforce targets for recycled plastic content.
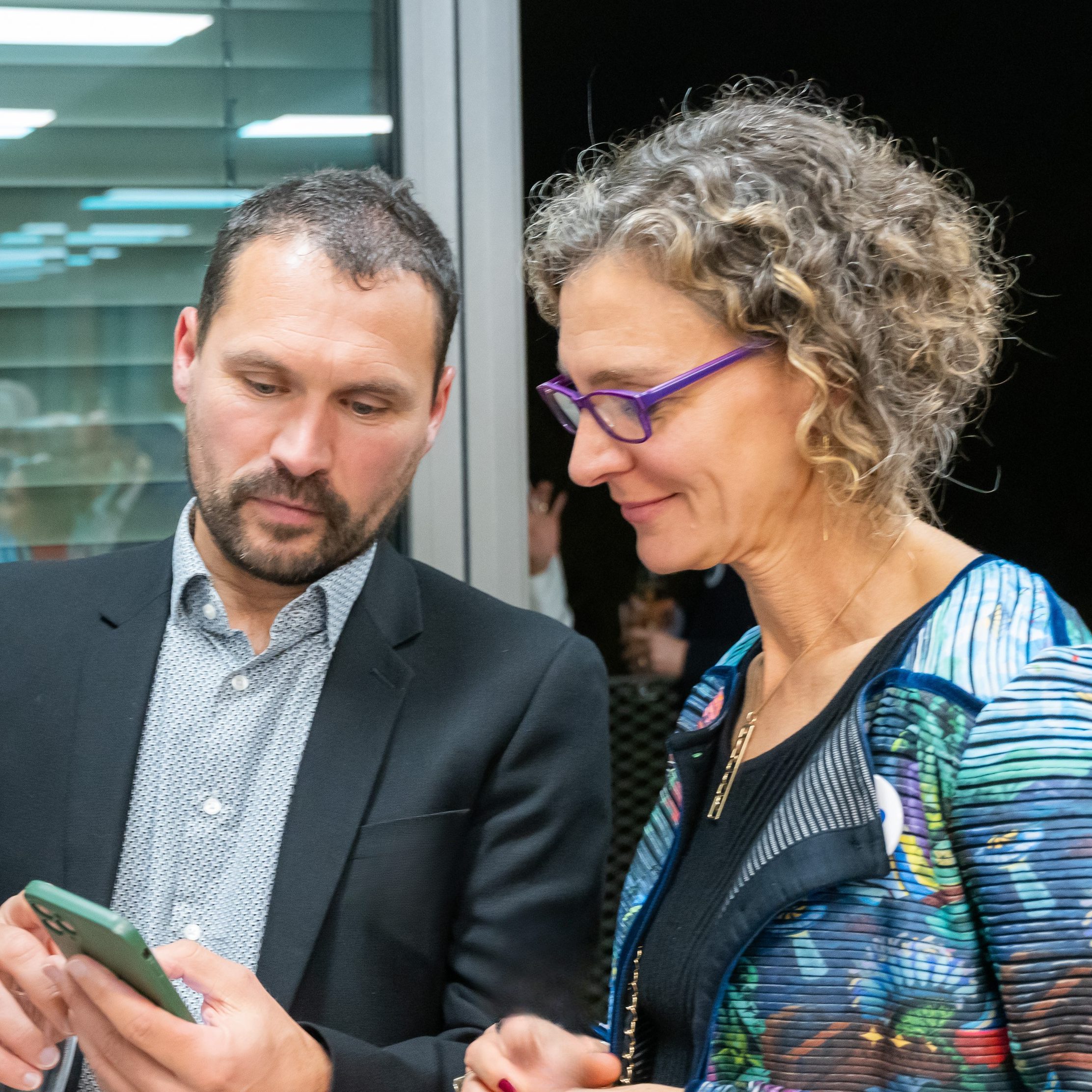
03. What’s next?
Standards matter.
There’s still plenty to do to develop industrial standards and specifications that seamlessly integrate environmental criteria. By working together, we can continue to make materials and products with environmental performance at their heart, as well as the tools and processes to define, assess, certify and trace products – like the Digital Product Passport – to ensure everyone is playing by the (same) rules.
Keen to join us on this zero-carbon journey?
We’re always looking for new partners and customers to help us create fossil-fuel alternatives
to high performance standards, which can be (and are) recycled
A few challenges on the way.
The road to net-zero and zero new plastic is going to get bumpy at times. But that’s the only road we care to take.
Wanna join us?
Pick a challenge you’d like to tackle with us.